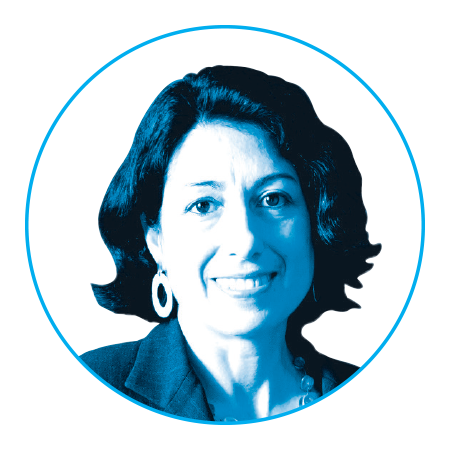
_Mimi Sheller
Sheller is director of Drexel’s Center for Mobilities Research and Policy and a professor in the College of Arts and Sciences.
In a world that is constantly on the move, Mimi Sheller studies the systemsthat make progress possible, for better and for worse.
As the director of Drexel’s Center for Mobilities Research and Policy and a professor in the College of Arts and Sciences, her broad research and publications provide a deeper understanding of the forces that shape the way modern societies travel, communicate and consume.
Sheller is president of the International Association for the History of Transport, Traffic and Mobility and co-editor of Mobilities, a journal she co-founded in 2006 to delve into the interdisciplinary field of study she helped establish. She is author and co-editor of nine books, including the monographs “Aluminum Dreams: The Making of Light Modernity” and “Citizenship from Below.” She is currently completing two new books, “Mobility Justice: The Politics of Movement in an Age of Extremes” and “Island Futures.” She is also working on a documentary with Jamaican film director Esther Figueroa on the global aluminum industry. This year, she delivered keynote addresses at conferences and workshops in Australia, Brazil, Canada, the Netherlands, Denmark and Italy, and gave the Society & Space plenary lecture at the American Association of Geographers Annual Meeting.
EXEL asked Sheller to expound on how society’s reliance on materials like aluminum play into the way we live.
Q: In your book “Aluminum Dreams,” you write about how aluminum shaped the 20th century as it became ubiquitous. How did it open up new possibilities for progress in the modern world, and is that changing in the 21st century?
A: The electricity grid, the buildings we live and work in, the satellites and gadgets we use to communicate, the way people and goods move from place to place, the power, speed, mobility and conveniences that we take for granted — all are made possible by aluminum. It underpins our material culture and our ideas of what it means to be modern. Aluminum first became available on a large scale in the early 20th century and quickly became a crucial material for streamlined vehicles, lighter packaging, mobile homes, new flight capabilities, high-tech military technologies, and the dawn of the Space Age. In addition to literally putting the world in motion, these new practices of mobility also generated visual representations and aesthetics of aerodynamic speed, accelerated mobility and technological futurism. By the 1950s, the gleam of aluminum surfaces was found on everything from Airstream trailers to kitchenware, and from rockets to airport lounges.
Today it remains a crucial material in new cars, food packaging, laptop computers, building construction and, of course, airplanes, spaceships and satellites. In some ways it has been eclipsed by the novelty of new materials such as titanium, carbon composites and nanomaterials (although some of these still make use of aluminum); yet we still depend on aluminum all the time in more mundane ways, such as for sports equipment (bikes, boats, bats); medical equipment (crutches, walkers, artificial limbs); and things like chairs, ladders and window frames. Look around and you will probably see some aluminum!
Q: In your book “Aluminum Dreams,” you write about how aluminum shaped the 20th century as it became ubiquitous. How did it open up new possibilities for progress in the modern world, and is that changing in the 21st century?
A: The electricity grid, the buildings we live and work in, the satellites and gadgets we use to communicate, the way people and goods move from place to place, the power, speed, mobility and conveniences that we take for granted — all are made possible by aluminum. It underpins our material culture and our ideas of what it means to be modern. Aluminum first became available on a large scale in the early 20th century and quickly became a crucial material for streamlined vehicles, lighter packaging, mobile homes, new flight capabilities, high-tech military technologies, and the dawn of the Space Age. In addition to literally putting the world in motion, these new practices of mobility also generated visual representations and aesthetics of aerodynamic speed, accelerated mobility and technological futurism. By the 1950s, the gleam of aluminum surfaces was found on everything from Airstream trailers to kitchenware, and from rockets to airport lounges.
Today it remains a crucial material in new cars, food packaging, laptop computers, building construction and, of course, airplanes, spaceships and satellites. In some ways it has been eclipsed by the novelty of new materials such as titanium, carbon composites and nanomaterials (although some of these still make use of aluminum); yet we still depend on aluminum all the time in more mundane ways, such as for sports equipment (bikes, boats, bats); medical equipment (crutches, walkers, artificial limbs); and things like chairs, ladders and window frames. Look around and you will probably see some aluminum!
Q: HOW DOES OUR RELIANCE ON ALUMINUM IMPACT OUR ENVIRONMENT AND HEALTH?
One-twelfth of the earth’s crust is aluminum, making it the third-most-common element after oxygen and silicon, but it is extremely difficult to get it into pure form. The main source is bauxite ore, which is first processed into alumina, and then smelted into aluminum. Bauxite mining is an open-pit process that leads to deforestation and leaves behind toxic “red mud” lakes.
To quantify it, each ton of aluminum produced requires four tons of bauxite ore to be strip-mined, crushed, washed and refined into alumina, creating about four tons of caustic red mud residue, which can seep into surface and groundwater. Dust from aluminum refining causes respiratory damage, and portside alumina spills have damaged coral reefs.
Aluminum smelting is one of the most energy-intensive production processes on earth. Smelting uses an electrolytic process in which a high current is passed through dissolved alumina. The electrochemical smelting of aluminum from refined bauxite ore requires between 13,500 and 17,000 kilowatt-hours of electricity per ton, more energy than any other kind of metal processing. To put this in perspective, making one soda can is said to require the equivalent of one-quarter of the can’s volume in gasoline to produce.
Because of its high demand for electricity, the process of producing aluminum creates on average 13 tons of carbon dioxide emissions per ton of aluminum. The aluminum industry emits about 1 percent of global emissions of man-made greenhouse gases. Smelters are also responsible for 90 percent of all tetrafluoromethane, and 65 percent of all hexafluoroethane emissions worldwide. These perfluorinated compounds have global warming potentials that are 6,500 to 9,200 times higher than carbon dioxide. Communities living near the industry around the world have increased asthma levels near bauxite mines, indications of multiple-chemical sensitivity around alumina refineries, and exposure to toxic waste such as fluoride and cyanide near aluminum smelters.
Some people also believe that ingesting or absorbing aluminum has human health impacts. It is not only found in our kitchenware and food packaging, but also occurs in powdered form in many cosmetics and deodorants, and is an adjuvant in vaccines. Accumulations of aluminum have been found in the brain tissue of people suffering from Alzheimer’s disease and have been connected to other neurological disorders, as well as showing possible links to breast cancer.
Q: WHAT COULD BE DONE TO LIMIT WASTE AND MITIGATE SOME OF THE CONSEQUENCES OF ALUMINUM MINING?
Architects, designers and engineers today still embrace aluminum as a sustainable “green metal” because of the energy efficiencies it enables, despite the pollution and human rights violations coincident with the industry around the world. In many places there are protests against the industry, including at bauxite mining areas in India, Guinea and Jamaica, and against smelters in Trinidad, South Africa, Canada and Iceland.
There are several ways that industry and citizens can try to mitigate these negative impacts. First, we could recycle all the consumer products we use with aluminum in them, especially cans. Melting down used aluminum requires only 5 percent as much energy as making it from ore. No one should ever put an aluminum can in the trash. We also need to simply use the metal more efficiently, insist on building with recycled aluminum, make products in which various metals can easily be separated out at the end of their lifecycle, and recover as much as possible from already-existing sources, such as so-called “urban mining,” which digs through landfills.
Beyond that, though, we also need to regulate the industry more carefully so that it doesn’t just move to places with little protection and get away with environmental and human rights violations. There are voluntary programs like the Extractive Industries Transparency Initiative, which enrolls countries in reporting on companies operating in their territory.
But we also need to ask ourselves when we buy a product: Where did this come from and how did it get there? Who is affected by the materials in the products I am using? We need to put pressure on companies to be more transparent about what they are doing, where they are doing it, and how they are treating both workers and surrounding communities.
Q: AS A SOCIOLOGIST, WHAT ROLE DO YOU BELIEVE THE SOCIAL SCIENCES CAN PLAY IN UNDERSTANDING HOW TO BALANCE THE BENEFITS AND HAZARDS OF THESE MATERIALS?
In my own work, I have tried to make people more aware of their involvement in larger systems of circulation of materials, whether it’s aluminum, the movement of energy or the impacts of tourism. Technology never operates on its own, but is always about how people use it, how we put things together and make them work.
If we want to make changes in complex systems we first have to be aware of them, but then we also need to develop specific and local forms of interaction, disruption or envisioning alternatives. This could take the form of citizen science, participatory art projects, community workshops to deliberate over new solutions, or community-based action research.
I am currently working with Jamaican filmmaker Esther Figueroa on a documentary called “Fly Me to the Moon” that will try to bring together audiences in different parts of the world to understand how they are connected by aluminum. I have often worked with artists, for example, to creatively engage people to think about their context differently or to link disparate groups together. And my forthcoming book “Mobility Justice” seeks to develop policies for greater equality and justice in all kinds of mobility systems, from the scale of the body, the street and the city to extended infrastructures and planetary ecologies.
At a recent conference of the International Association for the History of Transport, Traffic and Mobility (of which I am president) our theme was “Mobile Utopia: Pasts, Presents and Futures.” We conducted an arts exhibition, as well as “mobile utopia experiments” in which we invited groups of people to enact different ways of moving.
Q: DO YOU FEEL PESSIMISTIC OR OPTIMISTIC ABOUT THE DIRECTION THAT MATERIAL PRODUCTION WILL TAKE HUMANITY?
I am both pessimistic about the current system of material production and also optimistic over the longer term that we will be forced to make a change because we will have to. This is what the futurist Buckminster Fuller called “emergence by emergency.”
When the current system stops working (whether because of climate change disruptions, energy shortages or social conflict), we will need to find more energy-efficient and less wasteful ways of doing things. In the meantime, it is important to continue to develop alternatives — not only alternative technologies but also alternative social practices — as the foundations for a new socio-technical system to evolve.