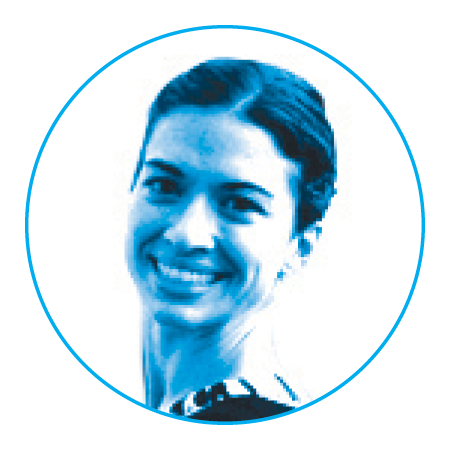
_Leslie Lamberson
Lamberson is an assistant professor in the College of Engineering in the Mechanical Engineering and Mechanics Department, with a joint appointment in Materials Science and Engineering.
If you truly want to know what something is made of, you push it past its breaking point, or so the adage goes.
That’s the idea behind Leslie Lamberson’s Dynamic Multifunctional Materials Laboratory, a one-of-a-kind materials testing lab she built from scratch for the purpose of, basically, breaking things.
“We push materials to their extremes to get a better understanding of their behavior under complex, real-world loading conditions,” says Lamberson, an assistant professor in the College of Engineering. “If you know how something breaks, that knowledge informs design. You can tailor it to break in a certain way, or even not to break by understanding its dynamic properties.”
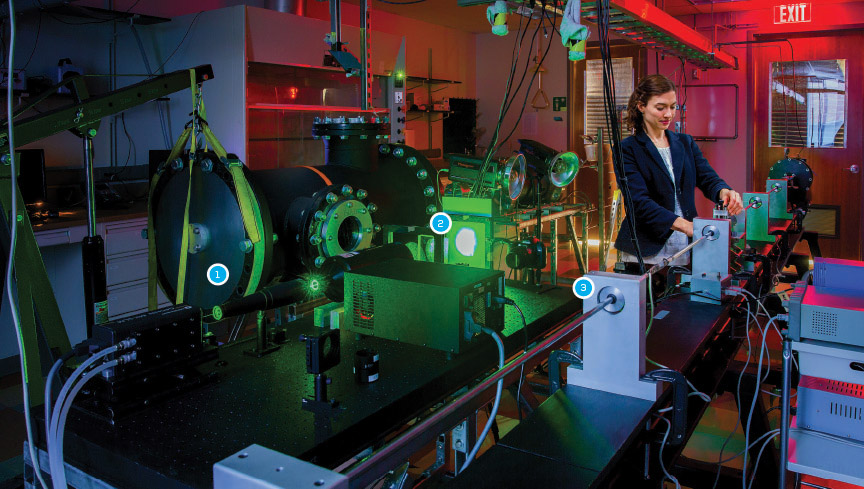
1. TARGET_PRACTICE
This patented two-stage light-gas gun can propel a projectile into a target at hypervelocity speeds of over 7,000 mph. Lamberson personally designed the machine for around $30,000, which is approximately how much it costs to run the NASA Ames Vertical Gun Range (a similar facility) for just one week. Lamberson uses the device to create micrometeoroid, orbital debris, and asteroid impacts within her lab. Plus, the first stage of the two-stage gun can be used individually as a blast tube to replicate the pressure profiles of an IED explosion on the battlefield — information that she’s using to propose ways to improve the protective foams inside soldier’s helmets with the Office for Naval Research.
2. LASER_FOCUS
The green laser light here is used as a lighting source while testing and photographing hypervelocity impacts, because regular white light does not have enough focused intensity to illuminate impact for the high-speed camera (to the right of the laser) to catch. The camera can take images up to 1 million frames per second, allowing it to capture all stages of damage evolution in order to understand how deformations, accelerations and fracture properties of growing cracks evolve under stress. “Using digital image correlation and other full-field optical diagnostics, we can get critical information on quantitative mechanical properties while the material is failing; and this information can be used to aid in the design of next-generation materials and structures,” Lamberson says.
3. STRESS_BEAM
This 20-foot Kolsky bar, also known as a split-Hopkinson pressure bar, is used to measure how materials respond to dynamic strain rates. A researcher would place a material to be tested between two long cylindrical bars, and then use a short projectile bar to strike the uprange end, to create a stress wave that propagates through the test material. Lamberson uses the device to study the effect of rate-dependent compression and confinement on materials, and also has the capability to electrically load and measure the stress and strain of a material under these extreme loading conditions. The equipment can be used with either two 9-foot steel bars to study hard materials like ceramics and rocks, or polycarbonate bars to examine soft materials like rubbers and foams.
To keep costs down and creativity and capability high, Lamberson designed and built — and even patented — most of the equipment in her lab using Drexel’s Machine Shop and, in some cases, spare parts she acquired from eBay, Craigslist and even Ikea.
Lamberson’s research so far has included replicating asteroid impacts; designing protective gear for soccer athletes and soldiers; examining cortical bone fractures; and testing tungsten carbide, one of the hardest metals known to man, for use in drill bits.